Nylon Tube VS PU Tube - How Do They Differ?
When it comes to pneumatic tubing, two names pop up quite often – Nylon Tube and PU Tube – also known as Polyurethane Tubing.
As a result, both are popular choices in various industries, thanks to their unique properties, specific application uses, and manufacturing processes.
Nylon, for example, is a synthetic polymer made from raw materials like petroleum, while PU tubing is produced from polyurethane – which is known for its flexibility and resilience.
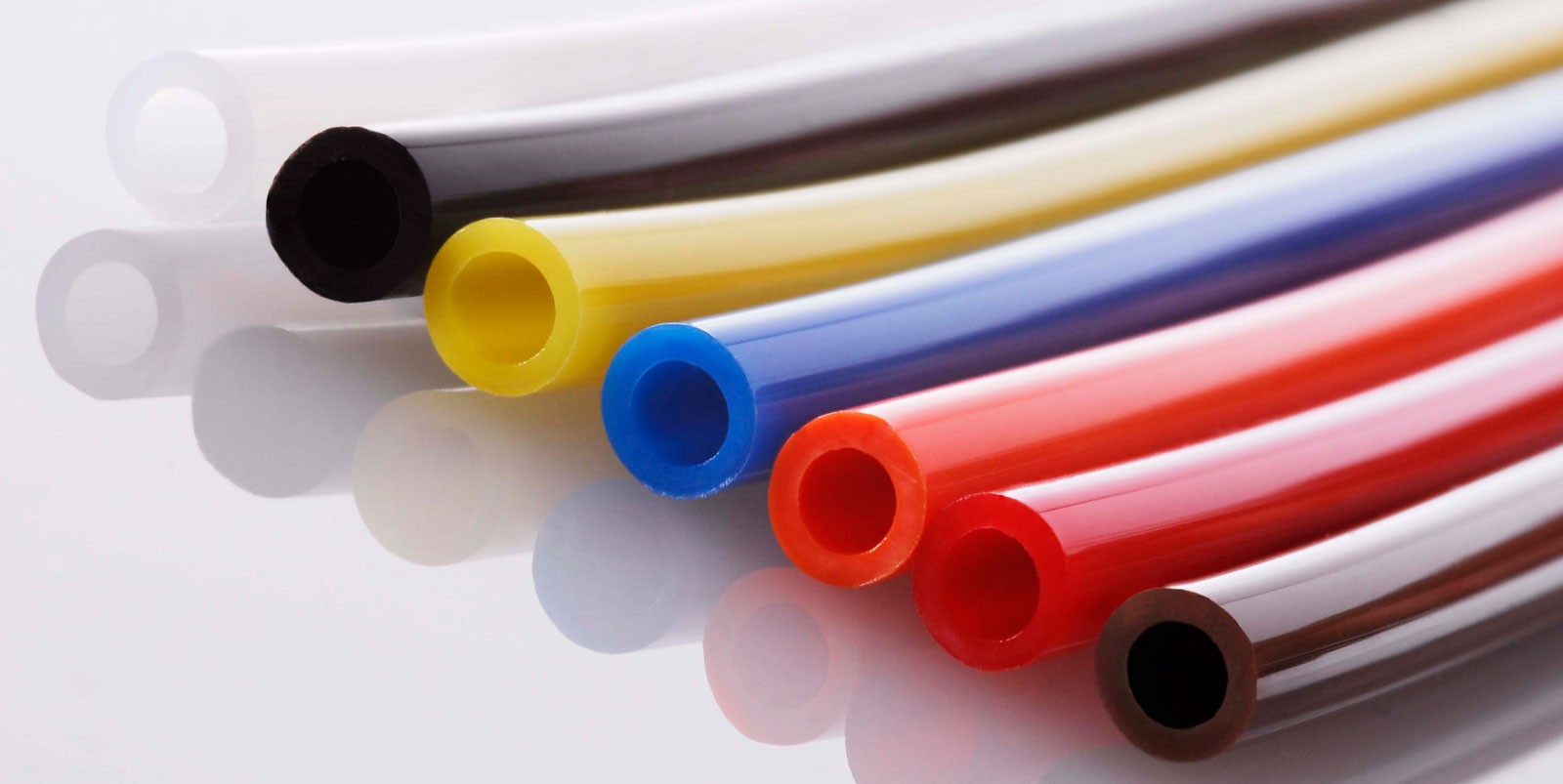
Common Use Cases For These Different Types of Tubes
You will often see Nylon Tubes are used in more high-pressure applications like hydraulic lines and fuel lines, along with applications that can see lower temperatures.
On the other hand, PU Tubes are found in tubing applications such as pneumatic tools, packaging systems, and even medical devices and have higher temperature tolerances as well. Another main reason here, is their excellent flexibility and bend radius properties, making them perfect for use in tight spaces and for a wide range of applications as a result.
Material Characteristics
When it comes to their material characteristics, here they can vary in a few ways, including, for example:
Nylon Tube’s Features and Benefits
Nylon tubing gives you excellent resistance to abrasion and low temperatures, making it a solid choice for harsh environments and environmental factors. As a result, it is often used in air lines, fuel systems, and industrial applications where strength really matters.
Nylon’s stiff overall structure also means it maintains its shape well under load as well, we should note.
PU Tube’s Features and Benefits
PU tubing then shines in areas requiring excellent flexibility and a soft touch. For example, it is commonly used for pneumatic applications where movement is more frequent and can easily accommodate stainless steel fittings easily as well.
Polyurethane hoses are also resistant to kinks, making them great for more dynamic applications and robotic arms due to this property.
Strength and Pressure Resistance
When it comes to their strength and pressure resistance, here you have a lot of variations in these as well, including, for instance:
Burst Pressure Ratings
When it comes to burst pressure, Nylon Tube takes the lead here.
This is because it is built to withstand higher pressures, making it ideal for hydraulic systems and high-pressure applications as a result.
PU tubing also performs well too, but is generally better suited for medium-pressure environments on the whole.
Load Handling
For load handling, you will tend to see that Nylon handles heavy loads better due to its rigid structure, making it a go-to in the automotive industry and industrial settings as a result of this.
PU tubing, while not as strong, still performs well in less demanding tasks where flexibility is key, though it is just not as good as Nylon can be on the whole.
Flexibility and Bend Radius
When it comes to their flexibility and bend radius, here they differ in a number of ways, such as for example:
PU’s Superior Flexibility
PU Tube is known for its excellent flexibility, especially in cold temperatures, and this makes it perfect for tight bends and complex routes in machinery as a result.
That is one reason you will tend to see it widely used in robotics, automation, and food processing applications.
Nylon’s Stiff Structure
Nylon Tube is not as flexible as PU, which makes it a bit tricky for installations that require tight curves. However, its stiffness is an asset in systems needing firm tubing that won’t collapse or deform under pressure.
Temperature Resistance
For their temperature resistance here, the main differences are around:
Nylon’s High Temp Tolerance
One of the key strengths of Nylon Tubes is their ability to handle high temperatures. This makes them perfect for applications with heat resistance needs, like fuel lines and hot air systems, and their temperature range is ideal for extreme temperatures found in industrial processes as well.
PU’s Moderate Temp Range
PU Tubing can also handle moderate temperatures quite well but may struggle under extreme heat. Consequently, it works best in environments where cold temperatures or room temperatures are the norm, like air conditioning and pneumatic systems.
Abrasion and Wear Resistance
For their abrasion and wear resistance properties, here we have for example:
How Nylon Handles Friction
Nylon gives you more excellent abrasion resistance, which is why it’s used in harsh environments with lots of movement or friction more often.
As a result, it tends to last longer in rugged settings like construction and heavy machinery due to this.
PU’s Resistance in Dynamic Applications
On the other hand, PU tubes also provide resistance to wear, especially when there’s a lot of movement involved.
This makes it more often chosen for dynamic pneumatic applications where tubing needs to bend and move continuously due to this as well.
Moisture Absorption and Water Resistance
For their moisture absorption and water resistance properties, here they can differ in a number of ways, including:
Nylon’s Hygroscopic Nature
Nylon is well known to be able to absorb moisture from the environment, which can affect its performance slightly, and this is something to keep in mind for outdoor or damp environments.
PU’s Better Moisture Resistance
The success of many products often resides on the impact of the environmental conditions associated with the application. Careful consideration should be given to not only the forces of an application, but also the environmental conditions. Specific combinations of conditions can result in problems such as rapid hydrolysis, discoloration, accelerated aging and cracking.
Chemical Compatibility
For their chemical compatibility, here they differ by:
Exposure to Oils, Fuels, and Solvents
Nylon for example, gives you excellent chemical resistance, especially against oils and fuels, and it is a great option for automotive applications and environments where chemical exposure is more common due to this.
Which Tube to Use in Harsh Environments
Consequently, if you are dealing with lots of chemicals, PU Hose is also a solid option. That is because it has excellent chemical compatibility and is suitable for various applications, including cleaning systems and lab environments.
Weight and Density
When comparing their weight and density, here we have:
Lighter Tube for Mobile Applications?
PU Tubing is generally lighter than Nylon, which makes it better for mobile setups and lightweight machinery due to this.
It also helps to reduce your overall load without sacrificing too much on performance as well here.
Comparison in Density
As a result, Nylon is denser and therefore heavier – this can be beneficial in static or permanent installations where weight is not so much of a concern but durability is we should note.
Durability and Longevity
For their durability and lifespan, here they tend to differ by:
Lifespan in Demanding Applications
Nylon has a longer lifespan in demanding and high-performance applications, and as a result, it is built to last in rough and tough environments – which is why it’s used in fuel lines and heavy-duty setups, after all.
Performance Over Time
PU Tube also gives you a decent level of durability but may wear out faster in extreme temperatures – or under continuous mechanical stress faster.
Still, it should hold up well for most pneumatic and light-duty tasks on the whole.
Installation and Handling
When it comes to their installation and handling, here you will tend to see:
Nylon’s Rigidity During Setup
Installing Nylon Tubes can be a bit of a challenge due to their stiffness, and you will need to carefully route and support them during your setup, especially around bends.
PU’s Ease of Use
PU Tubes, on the other hand, are much easier to work with, as their flexibility means you can bend and route them with minimal effort – making installation faster and simpler as a result of this.
Applications by Industry
Where they are used can also differ, for example:
Nylon in Automotive and Pneumatics
Nylon Tubes are used extensively in the automotive industry for fuel systems, brake lines, and air conditioning, and they are also key in high-pressure pneumatic systems as well.
PU in Robotics and Packaging
PU Tubes, on the other hand, are widely used in robotics, packaging, and automation systems due to their flexibility, and they are also found in the food and medical sectors, thanks to their chemical resistance, the fact that they are safe for food processing and easy to handle as well.
Comparison Table of Nylon Tube vs PU Tube
Feature | Nylon Tube | PU Tube (Polyurethane) |
---|---|---|
Flexibility | Rigid, less flexible | Very flexible, great for tight bends |
Pressure Resistance | Excellent for high-pressure applications | Good for medium-pressure systems |
Temperature Resistance | Handles higher temperatures well | Best for moderate to low temperatures |
Abrasion Resistance | Excellent in harsh environments | Very good, especially in moving parts |
Moisture Absorption | Can absorb moisture (hygroscopic) | Low water absorption, water resistant |
Chemical Compatibility | Great with fuels, oils, and solvents | Good with many chemicals |
Weight | Heavier | Lighter |
Ease of Installation | Stiffer, trickier to install | Very easy to install and handle |
Durability | High durability and longevity | Good for less extreme environments |
Typical Uses | Automotive, fuel lines, air brakes | Robotics, packaging, pneumatic tools |
Cost | Higher initial cost | Budget-friendly upfront |
Environmental Impact | Harder to recycle | More eco-friendly and recyclable |
Nylon Tube vs PU Tube Final Thoughts
As you can see both of these types of tubing have different properties and use cases. For example, you should consider choosing Nylon if you need a tube that can handle higher pressures, extreme temperatures, and harsh environments, and it is also perfect for automotive, hydraulic, and heavy-duty pneumatic applications.
On the other hand, you should consider picking PU for its flexibility, ease of use, and suitability in light-to-medium duty pneumatic systems, and the fact that it is also great for robotics, packaging, and applications with lots of movement and tight spaces as well.
If you still need help knowing which one is right for your application, though, our team is on hand to help you as well – so please do not hesitate to get in touch.
Other Types Of Tubing
If you are considering this, other types you should or you may be interested in considering include, for example:
Bespoke
Can't find the right tube to meet your unique requirements?
We have decades of experience in creating custom tube solutions for a wide range of industries, ranging from the pharmaceutical industry to the aeronautics sector.